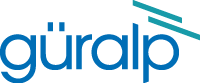
Chapter 5. Inside the 3V / 3ESPV
5.1 The sensor
The inertial mass of the sensor consists of a transducer coil and a leaf-spring suspended boom which swings on a frictionless hinge. A triangular spring supports the weight of the mass; this spring is pre-stressed, with a natural period around 0.5 s.
The sensor and hole lock units are stacked one on top of the other with a set of accurately-machined stacking tubes, which also form part of the sensor's pressure housing. Fixing holes provided on each end face allow for simple and accurate assembly. The base of each unit includes a double “O” ring to isolate the sensor from any pressure variations in the atmosphere.
The 3V and 3ESPV function by monitoring the position of the mass with a capacitative position sensor. Signals from the sensor are fed into an electronic processing unit, which is mounted in a screened compartment above the mechanical components (see below for details on the feedback circuitry.)
When the instrument is being transported, the sensor mass is locked securely in its frame so as to relieve strain on the support hinges. This locking is performed by a small motor-driven clamp in response to a signal from the surface controller unit.
Before using the instrument, the boom of the sensor must be levelled so that its mass is centred in its equilibrium position. These adjustments are made by a small DC motor controlled remotely.
See Chapter 3, page 22, for detailed instructions on how to set up your installation.
The signal voltages output by the instrument are proportional to ground velocity, and are transmitted from the instrument on balanced differential lines. In addition, mass position signals are sent as single-ended circuits referred to analogue ground on the output plug. The 3V also receives control signals, which are used to clamp and unclamp the masses, and to run the motors which level and centre the instrument once in position. Finally, a line is provided for you to apply a calibrating voltage to the force transducers, thereby measuring the deflection sensitivity.
5.2 The control system
The internal operations of the sensor are supervised by a control microprocessor, which drives the mass clamping and centring adjustment motors. It responds to commands sent on three input lines by grounding for 0.2 – 7 seconds.
The signals you can send to the microprocessor are termed LOCK, UNLOCK, and CENTRE. The microprocessor prevents the system from attempting incompatible actions (e.g. centring when the masses are clamped.)
While a command is taking place, if you are using a Handheld Control Unit, its BUSY LED will flash; you can use this for diagnostic purposes. See the description of each command for full details.
When no command is active, i.e. all three lines are high, the control microprocessor goes into a power-saving mode. In routine operation, the lines are controlled from the breakout box, Handheld Control Unit or digitizer. If you send control signals to the 3V manually, you must ensure that the lines are pulled high after sending the signal, or the equipment may be damaged. A “biased-OFF” type switch can be used for this purpose.
This command locks the mass in position, ready for transportation.
If LOCK is activated when the mass is already locked, the processor will unlock it and attempt to lock again. This is useful if you suspect that the locking procedure has failed.
The BUSY LED is lit whilst locking is in progress.
This command unlocks the sensor mass and prepares the instrument to begin operating.
If UNLOCK is activated when the mass is already unlocked, the processor will lock it and attempt to unlock again. This is useful if you suspect that the locking procedure has failed.
During the UNLOCK procedure, the instrument automatically performs a round of centring. You can use the BUSY LED to monitor the progress of unlocking:
The instrument checks to see whether the mass is locked, and unlocks it if necessary.
The mass is centred by applying pulses to the motor. This stage is often very short, since the vertical mass is locked near its central position.
This command re-centres the mass. If the mass is clamped, or if the sensor mass position does not exceed ± 1.2 V, the CENTRE command does nothing. Otherwise, it attempts to zero the output of the sensor. by exerting small extra forces on the boom. A motor-driven adjuster presses a small spring lever against the boom until the mass position sensor indicates an offset close to zero.
The BUSY LED will pulse whilst the mass is centred. The centring process is often very short, since the vertical mass is locked near its central position.
After successful centring, the mass position output should be in the range 0.1 – 0.8 V. If the centring process leaves the mass position output above ±1.1 V, you should start another centring cycle by activating the CENTRE command again.
5.3 The feedback system
The output from a modern broadband seismometer does not depend on the natural characteristics of the instrument. Instead, the period and damping of the sensor is completely determined by a feedback loop which applies a force to the sensor mass opposing any motion. The force required to restrain the movement of the mass can then be used to measure the inertial force which it exerts as a result of ground motion.
All CMG-3 series units are based on these general principles. The capacitative position sensor for each mass produces a voltage proportional to the displacement of the mass from its equilibrium position. After amplification, this voltage generates a current in the force transducer coil which tends to force the mass back toward equilibrium. The feedback loop has a sufficiently high gain to cancel the motion of the mass. Since the mass is not moving, the forces acting on it must be balanced; the feedback voltage then directly measures the force, and hence the acceleration, which is being applied to the mass. The feedback loop introduces a phase shift, which must be carefully controlled if the instrument is to remain stable over its entire frequency range. This is achieved using compensation components in the forward and feedback paths.
Force feedback seismometers of this type rely on the assumption that the force transducer produces a field of constant strength. The magnetic circuit and magnet/pole assembly in the 3V and 3ESPV are designed so that the field strength from the feedback transducer is constant over large deflections and current levels. Tests have shown that the mechanical suspension system and electronics of a 3V instrument are linear to better than 107 dB (source: measurements made at ASL during evaluation for the USGS National Network.)
In a feedback seismometer with a displacement transducer, it is essential to monitor the acceleration output. This provides the position of the displacement transducer and therefore also the mass position, as the displacement transducer is attached to the sensor inertial mass. The sensor should always be operated with the displacement transducer centred or nulled, so that the response to input acceleration is linear.
There are two types of feedback system which can be used in a CMG-3 series instrument, known as hybrid and conventional-response feedback.
The hybrid feedback circuit contains a single capacitor in parallel with a resistor, resulting in a single dominant pole at 0.033 Hz (30 s). Below this frequency, the response of the seismometer is flat to ground acceleration; above it, the response is flat to velocity. (Other values for the acceleration-velocity corner can be provided upon request.) Hybrid-feedback systems provide a stable response, particularly for portable systems, with a high saturation level at high frequencies and a high dynamic range at long periods.
An active low-pass filter provides a high-frequency cutoff point at a frequency you specify. Without the filter, the velocity response is flat up to 100 Hz. Outside the feedback loop there is an active high-pass filter with a corner frequency of 0.01 Hz (100 s) or 0.005 Hz (200 s), which serves to remove any DC offsets.
Conventional-response feedback
The conventional-response feedback system has an additional parallel feedback circuit, consisting of a non-inverting integrator in series with a resistor. This arrangement results in two poles at specified frequencies. The velocity response of a conventional-response system is defined by a transfer function identical to that of a conventional long-period sensor with a damping constant ζ of 0.707 (1/√2)
The seismometer can be supplied with an equivalent resonant frequency of 0.033 Hz (30 s), 0.01 Hz (100 s) or 0.0083 Hz (120 s) as required. An active low-pass filter provides a high-frequency cutoff point at a frequency you specify.
The figures below plot the comparative response of a conventional velocity output broadband sensor and a hybrid output broadband sensor. The upper graph shows the response in terms of output against input acceleration in units of V/m/s2, whilst the lower graph is plotted in terms of output against input velocity, in V/m/s.