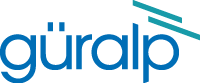
Chapter 3. First encounters
3.1 Unpacking and packing
The 3TB seismometer is delivered in a single transportation case, with the sensor system and hole lock mechanism (if ordered) packed separately. The packaging is specifically designed for the 3TB and should be reused whenever you need to transport the sensor. Please note any damage to the packaging when you receive the equipment, and unpack on a clean surface.
The package should contain:
the seismometer;
a cable to join the sensor to the breakout box;
the breakout box;
the hole lock control unit (optional);
a cable strain relief mechanism or combined cable strain relief mechanism and surge suppressor;
a Hand-held Control Unit (HCU) for monitoring sensor outputs and calibration, if ordered; and
a calibration data sheet.
The sensor is securely packed, and you will need to remove most of the foam packing before it can be removed.
3TBs used to be delivered in sections which had to be assembled by the user. They are now shipped complete and no assembly is required. If you are working with a disassembled unit and need assembly instruction, please contact support@guralp.com for an earlier version of this manual. If you need to transport a unit but the packaging you have requires disassembly of the instrument, please contact support@guralp.com for an up-to-date shipping container.
3.2 Handling notes
The 3TB is a sensitive instrument, and is easily damaged if mishandled. It will not stand vertically upwards without support, and should not be operated until it has been securely installed in a borehole casing. If you are at all unsure about the handling or installation of the device, you should contact Güralp Systems for assistance.
Do not bump or jolt any part of the sensor when handling or unpacking.
Keep the sonde sections vertical wherever possible. Carry them by hand and store in a safe rack. Never drag or roll the sonde.
Never lay the sonde horizontally whilst the sensors are unlocked. If the sensor system topples over, you must inform Güralp Systems.
Keep all the parts of the sensor system protected and clean so that they can be joined together securely. Store in the original packaging if possible.
Do not kink or walk on the data cable (especially on rough surfaces such as gravel), nor allow it to bear the weight of the sensor.
Do not connect the instrument to power sources except where instructed.
3.3 Control units
The 3TB is operated from the surface through various control units. All the 3TB's functions can be accessed through one or other unit. Most can be removed from the site once the instrument is ready for use.
Some of these control units are optional and may not have been supplied with your installation. Their functions can be duplicated either by directly grounding control lines (see appendixes for pin-out information) or through a connected Güralp digitizer such as the Güralp DM24. The DM24 digitizer is able to pass commands to the instrument from an Enhanced Acquisition Module (Güralp EAM) or a computer running Güralp Systems' Scream! software, allowing you to access all of the instrument's functions remotely.
3.3.1 The break-out box
The break-out box is normally placed where the signal cable emerges from the borehole. It provides connectors for attaching the various other control units, supplies power to the instrument and relays output signals to a recorder or digitizer. It is not required when a down-hole digitiser is used.
The SENSOR connector is a 26-way military-specification bayonet plug, and should be connected to the borehole instrument using the cable provided.
The RECORDER connector is a 26-way military-specification bayonet plug. This should be connected to an analogue data recorder or stand-alone digitizer.
The CONTROL connector is a 26-way military-specification bayonet plug intended for connecting to an external controller or Hand-held Control Unit. It has the same pin out as the RECORDER connector.
The POWER connector is a 10-way military-specification bayonet plug, which should be connected to a source of 12 – 30 V DC power, for supplying to the borehole instrumentation. When operating the hole lock, you should connect the Hole-lock Control Unit to this connector. Because of the potentially high voltages and currents used, the hole lock circuitry is entirely isolated from the rest of the electrical systems in the sensor and surface unit; it is not usual to power the sensor whilst using the hole lock.
For deep-borehole installations (over 50 metres) may be necessary to use a modified instrument (with “active-high” logic ) and a breakout box with internal line drivers, to ensure that logic signals are reliably transmitted to the sensor. Contact Güralp Systems for advice.
Note: The breakout box looks very similar to other Güralp breakout boxes. However, its internal wiring is different from that used for some other instruments. For this reason, if you are using several instrument types, you should mark each breakout box clearly so that it is always used with the correct instrument.
3.3.1.1 Calibration
To calibrate the instrument, the Calibration enable line must be activated. This operates a relay which allows a calibration signal to flow through the transducer feedback coil. This provides an extra force acting on the sensor masses, producing a corresponding deflection in the output signal, which can be analysed by a control computer to extract the seismometer's response characteristics.
Most Güralp instruments are manufactured with “active-low” Calibration enable lines, which are normally left floating but are grounded to initiate calibration. Instruments with active-high calibration can be manufactured on request.
3.3.1.2 Mass locking and unlocking
The 3TB is delivered with its sensor masses locked, so that they will not be damaged in transit. You should lock the masses whenever you need to move the instrument.
To unlock the instrument, hold down the ENABLE and UNLOCK buttons (or the UNLOCK switch on a breakout box) for at least six seconds. The sensor's microcontroller will free the vertical, N/S and E/W sensor masses in turn and ready them for use. Once this is done, the controller automatically starts a centring cycle. If you issue an UNLOCK command when the masses are already free, the instrument will attempt to lock the masses first, and then unlock them in sequence as normal.
To lock the instrument, hold down the ENABLE and LOCK buttons (or the LOCK switch) for at least six seconds. The sensor's microcontroller will lock the vertical sensor mass, followed by the N/S and E/W sensor masses in turn. After this, the controller locks the base of the horizontal instrument, tilting it until it is held against its end stop. The instrument is now protected against accelerations up to 10g, and is ready for transportation.
3.3.1.3 Centring
To centre the instrument, hold down ENABLE and CENTRE buttons (or the CENTRE switch) for at least six seconds. If the masses are locked, the microcontroller will do nothing. Otherwise, it attempts to zero the output of the vertical, E/W, and N/S sensors in sequence by exerting a small extra force on the boom. For the vertical sensor, a motor-driven adjuster presses a small spring lever against the boom until the mass position output indicates an offset close to zero. In the case of the horizontal sensors, the sensor frame is tilted on its base plate. Again, the controller monitors the mass position sensor and stops the centring process once it reaches its lowest offset.
After successful centring, the mass position outputs should be in the range 0.1 – 0.8 Volts. If the centring process leaves the mass position outputs above ±1.1 V, start another centring cycle. You will probably need to perform several rounds of centring before the masses are ready.
3.3.2 The hand-held control unit
This portable control unit provides easy access to the seismometer's control commands, as well as displaying the output velocity and mass position (i.e. acceleration) on an analogue meter.
3.3.2.1
Connections
The HCU provides
two identical 26-pin, military-specification bayonet connectors for attaching to the HCU or RECORDER connectors of the breakout box, and
a 10-pin, military-specification bayonet connector through which you can power the instrument, if desired. The power pins on this connector are directly connected to those on the SENSOR POWER connector of the breakout box. When using this alternative power connection, you should ensure you do not inadvertently connect two power supplies together.
3.3.2.2 Signal meter
The upper section of the HCU contains a simple voltmeter for monitoring various signals from the instrument.
To monitor the velocity outputs, switch the dial to V, N/S or E/W VEL according to the component you want to monitor.
To monitor the mass position outputs, switch the dial to V, N/S or E/W MASS POS according to the component you want to monitor.
You can set the range of the meter with the RANGE switch. When switched to 10 V, the meter ranges from –10 to +10 V (as marked). When switched to 1 V, the range is –1 to +1 V.
3.3.2.3 Calibration and control
You can calibrate a 3TB sensor through the HCU by connecting a signal generator across the yellow and green CALIBRATION SIGNAL inputs. The CAL ENABLE dial must be set to 'V' – the 3TB has only one calibration enable line and this acts on all components simultaneously. The sensor's response can now be monitored or recorded, and calibration calculations carried out.
The section of the HCU below the calibration lines controls the instrument's mass control system. To initiate locking, unlocking, or centring, hold down the ENABLE switch on the HCU together with the appropriate switch for the command you want to issue for at least six seconds.
3.3.2.4 Banana plugs
The remainder of the HCU provides useful connections for each of the signal lines from the instrument, for attaching to your own equipment as necessary.
3.3.3 The inclinometer monitor unit
All 3TB borehole sensor systems can operate successfully in boreholes with tilt angles of up to 3.5° from the vertical although instruments which can operate at tilts of up to 12° are available – please contact Güralp Systems for details. To check that the instrument is installed suitably close to the vertical, a two-axis inclinometer is installed within the sensor housing. The inclinometer monitor unit is used as a visual guide to the sensor's tilt only, and should not be used if precise attitude information is required.
Caution: You should check the inclination of the instrument before unlocking the sensor masses, since too great a tilt can damage the components.
To measure the attitude of a 3TB instrument:
Connect the inclinometer monitor unit to the CONTROL connector of the breakout box.
Switch the ON/OFF switch on the monitor unit to the ON position. The inclinometer is powered separately from other parts of the system; this switch provides power to the downhole circuitry as well as to the monitor unit. The inclinometer should not normally be powered up whilst the sensor is in use.
Read off the X and Y components of the tilt from the analogue meters.
If both tilts are within the green shaded region, the instrument is close enough to vertical that it can be levelled and centred successfully. If either output is in the red shaded region, you should not attempt to unlock or centre the sensor masses. Instead, if possible, you should move the instrument within the borehole to a place where it can lie closer to vertical.
If you need to use the outputs of the inclinometer for some other purpose, you can also connect a multimeter to the banana sockets on the inclinometer monitor unit.
3.4 Operating the hole-lock
The hole lock, if fitted, can be extended and retracted using the hole lock control unit:
Warning: The hole lock may be using high-voltage mains (outlet) power.
To operate the hole-lock:
Connect the hole-lock control unit to the HOLELOCK POWER connector of the breakout box, and to a mains power supply. Alternatively, connect a 12 – 24 V DC power supply across the input terminals of the hole lock control unit.
Caution: Do not connect both DC and mains power at the same time.
The hole-lock control unit supplied in regions with 220 V AC mains power differs from that supplied for 110 V AC mains power. You should ensure that you provide the correct voltage to the hole lock control unit, otherwise damage may result to the sensor.
If you are using a deep-borehole hole lock control unit, set the dial to zero.
To extend the jaw of the hole lock:
Hold the switch on the hole lock control unit in the EXTEND JAW or + position. If you are using a deep-borehole control unit, there will be an additional dial compared to the unit pictured; turn this until the built-in ammeter reads around 0.1 A.
When the arm makes contact with the borehole casing, the current will drop slightly. Continue holding the switch in the EXTEND JAW position.
When the lock arm reaches its fully extended position, the motor will automatically stop and the current will drop to zero. If using a deep-borehole unit, return the dial to zero.
If the current has not dropped quite to zero after 30 – 40 seconds of operation, release the switch, wait a few seconds, and push it back to the EXTEND JAW position briefly. If the arm is not completely extended, you will see a surge of current. If the current remains constant, the jaw is at its maximum reach.
Once the sensor is locked in place, it is recommended that you remove the hole lock power cable and control unit from the site. Without power, the hole lock will not be able to retract, and the sensor will be secure.
3.4.1 Disengaging the hole lock
To retract the jaw of the hole lock:
Tension the load bearing cable, to take up any slack.
Hold the switch on the hole lock control unit in the RETRACT JAW or – position. If using a deep-borehole control unit, also turn the dial until the built-in ammeter indicates 0.3 – 0.5 A. More current is drawn retracting the arm, because the motor is now working against the spring.
When the lock arm reaches its fully retracted position, the motors will automatically stop and the current will drop to zero. If using a deep-borehole unit, return the dial to zero.
If you prefer, you can operate the hole lock by applying voltages directly to the sensor.
To extend the jaw, connect the Hole Lock Motor pin on the sensor (or on the breakout box's HCU or RECORDER connectors) to a +12 V power source, and the Hole Lock Motor Return pin to 0 V (ground).
To retract the jaw, reverse the polarity so that the Hole Lock Motor Return pin is at +12 V and the Hole Lock Motor pin is at 0 V (ground).
3.5
The surge suppressor sonde
3TBs can optionally be provided with an extra sonde, combining a surge suppression system with a cable strain relief arm.
The surge suppressor sonde has the same connector as the instrument on its top face and a short, permanently attached cable extending from the bottom, which connects directly to the 3TB. Internal electronics provide a high degree of protection from damage cause by electrical surges, as can arise during, for example, a nearby electrical storm. A combination of gas discharge tubes, metal-oxide varistors, zener diodes, inductors and capacitors helps prevent electrical surges from reaching the instrument.
Note that no surge suppression systems can offer total protection, especially in the event of a strike by a lightning bolt within a few tens of metres of the installation.
The bottom of the surge suppressor sonde has a spring-loaded metal arm which performs the same function as the strain-relief unit. The arm swings out from the bottom of the sonde to wedge against the side of the borehole. This removes any strain in the load-bearing cable and prevents vibrations from the surface from being transmitted to the instrument.
3.6 Using Baffles
Baffles are a useful tool to prevent convection currents in the borehole from generating low-frequency oscillations.
The baffle consists of some large, deformable washers and spacer material attached to a cable clamp. For best results, one should be installed on the signal & suspension cable, half way between the sensor and the surge arrestor. Once in position, it should be tightened onto the cable using the socket-head screws.