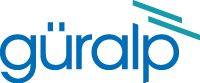
Chapter 3. Single sensor operation.
3.1 Set-up
3.1.1 Hole-lock skids
The instrument's hole-lock should be configured for the diameter of the bore-hole into which it is being deployed. Configuration is performed by changing the spacing pieces onto which the skids are mounted. The screws used to mount the skids should also be selected appropriately.
For each size of bore-hole, the skid spacers should be changed on both of the two spacers. Care should be taken with the length of screw used: the screw should not be so long that it interferes with the internal mechanics of the hole-lock or damage may occur resulting in inoperable hole-locks and failure of the pressure integrity of the sensor. As a guide, spacers may be set up depending on the bore-hole diameter as shown in the table below:
Borehole Size (mm) | Spacer Sizes (mm) | |
skid one | skid two | |
91-95 | 92.5 | 92.5 |
95-97 | 92.5 | 97.5 |
97-100 | 97.5 | 97.5 |
100-102 | 97.5 | 102.5 |
102-105 | 102.5 | 102.5 |
105-107 | 102.5 | 107.5 |
107-110 | 107.5 | 107.5 |
3.1.2 Orientation
The correct orientation of the instrument is identified by the hole-lock. The hole-lock is at the top of the instrument and the instrument should be rotated such that the hole-lock arm points Northwards.
3.1.3 Connections
When used in single sensor configuration, the supplied end-cap must be fastened to the bottom of the instrument. The end-cap provides essential environmental protection.
Caution: Deploying the instrument without the end-cap will result in poor vertical performance and moisture / water ingress, with consequential damage to the instrument.
The supplied 10 m sensor cable should be attached to the top of the instrument. Before attachment, the 'O'-rings should be inspected, cleaned and greased with a suitable, silicon-based grease.
Caution: Contaminated, damaged or poorly greased 'O'-rings can result in water ingress, with consequential damage to the instrument.
3.1.4 Suspension
Note that the supplied 10 m sensor cable has an integral lifting eye. When suspending the sensor from the cable, the lifting eye must be used to support the weight of the cable and sensor. Never use the bayonet connector for this purpose.
3.2 Deployment
3.2.1 Hole-lock operation
The hole-lock arm is driven by a 12-volt, bi-directional DC motor, with limit-switches to prevent the motor from being over-driven in either direction. The direction of travel (extension or retraction) is controlled by the polarity of a voltage applied to a separate control line. When the hole-lock arm is fully extended or fully retracted, the limit-switch acts to disconnect the motor from the supply lines.
Note: It is recommended that the operator familiarises themselves with the operation of the hole-lock before the sensor is deployed, taking note of the approximate times for deployment and retraction and the normal operating current. Excessive operating current indicates a stalled motor: the locking arm may be jammed in this case.
To operate the hole-lock:
Power: Apply +12V to pin V with respect to pin B.
Control: Apply ±12V to pin H with respect to pin Y. The polarity of the applied voltage determines the direction of movement.
3.2.2 Sensor operation
Single sensors may be powered from a 9-36 V DC power supply. The quiescent power consumption of a single sensor is less than 200 mW at 12 V.
The sensor provides some status information by pulsing pin K. This is referred to as the “busy line” and is used to drive the “busy” LED on the surface control unit.
When first powered up, the sensor will flash the busy line once, wait for ten seconds and then enter a hibernation mode. If a centring signal is received during the initial three seconds, the instrument will enter and automatic centring sequence, which takes around one minute. To send the centring signal, ground pin U ('CENTRE') to pin Y ('Digital ground') for between one and four seconds.
To deploy the instrument:
Secure the end-cap to the bottom of the sensor. This is essential to prevent ingress of moisture. The bottom of the sensor is the end opposite the hole-lock.
Caution: Deploying the instrument without the end-cap will result in poor vertical performance and moisture / water ingress, with consequential damage to the instrument.
Lower it into the bore-hole, taking care that all the weight is taken by the lifting-eye in the cable and not the upper connector.
Warning: The top connector and/or breakout cable should never be used to support the weight of the assembly. Use only the lifting-eye for this purpose.
When the required depth is reached, deploy the hole-lock until the operating current drops to zero (limit switch activated) or increases dramatically (motor stalled).
Check that the sonde is firmly anchored by increasing the tension on the cable for a short period. No movement should be noted other than the normal stretching of the cable.
Apply power to the instrument and allow three seconds for it to initialise. The busy line should flash once at power-up.
Ground pin U with respect to pin Y to initiate centring.
During the centring process:
The busy line will first flash rapidly for ten seconds and then go out for five seconds.
When the first component is centred, the busy line will produce a regular, single flash.
When the second component is centred, the busy line will produce regular, double flashes.
When the third component is centred, the busy line will flash three times then go out.
If manual centring is not initiated as above, the automatic centring feature will activate after around ten minutes.
Note: If the sonde is tilted more than 30° from the vertical, the horizontal components will not centre. If the sonde is tilted more than 60° from the vertical, the vertical component will not centre.
3.3 Operation
3.3.1 Control lines
The instrument is equipped with a number of control lines. These are TTL-level inputs which are floated to 5 V by internal resistors. To assert one of these lines, it should be grounded to pin Y ('Digital ground') as described in the following text.
Caution: Never connect any of these control lines to any voltage or current source. They must either be left floating (“high”) or connected to digital ground (“low”).
3.3.2 Centring
To wake and centre the sensor, ground pin U ('CENTRE') to pin Y ('Digital ground') for between one and four seconds. The sensor will switch into one-second response mode and check the mass positions. If any of the mass positions are over 25% of full-scale, the instrument will be automatically re-centred.
If the centre line is grounded for over five but less than fifteen seconds, the sensor will check the mass positions in which ever long period mode is currently selected and centre the instrument if the mass positions are over 25%.
3.3.3 The BUSY line
During centring, the busy line will be driven high periodically. If a suitable LED is connected it will flash repeatedly once when one component is centred, twice when two components are centred and three times when all three components are centred.
3.3.4 Response modes
The low-frequency corner of the instrument's response can be remotely configured by grounding pin S and/or pin T to pin Y ('Digital ground'). Four frequencies are available (expressed as periods): one, ten, thirty and sixty seconds.
To select the required frequency response, ground pins S and/or T to pin Y according to the following table. If not grounded, the pin should be left floating.
Desired response | Pin S | Pin T |
1 second, Short period | grounded | grounded |
10 second, Medium Short Period | floating | grounded |
30 second, Medium Long Period | grounded | floating |
60 second, Long Period | floating | floating |
3.3.5 Calibration enable
To enable a calibration signal to be injected into the sensor, pin R ('Calibration Enable') must be grounded to pin Y ('Digital ground'). The calibration signal should be injected via pin P. The signal passes though a 51 kΩ resistor, then through a 64 Ω feedback coil to pin N ('Signal ground').
3.3.6 Auto-centre
The instrument will continually monitor its mass positions and, if any mass position stays at or beyond 75% excursion for ten minutes, auto-centring is initiated.
3.3.7 Inclination monitoring
If the instrument is tilted over 30° from the vertical, the corresponding horizontal component will not centre.
If the instrument is tilted over 60°, neither the corresponding horizontal nor the vertical component will centre. If the sensor is maintained at such an angle and fails to centre, it will recheck the inclination every 12 hours to see if the tilt has changed. Auto-centring will then be initiated provided at least one mass position is over 75%.
3.3.8 Serial communication
Serial communication with the instrument's processor allows configuration of the frequency response and initiation of centring and calibration.
The serial port runs half-duplex RS485 in 8-bit mode at 38,400 Baud.
The instrument's processor is normally in a low-power “sleep” mode in order to reduce total power consumption. To wake the processor, ground pin U ('CENTRE') to pin Y ('Digital ground') for between one and ten seconds. A menu is displayed as below:
SENSORS : A_ll, V_ertical, N_orth, E_ast – centre
MODE : S_hortperiod, B_roadband
CONFIG : R_esponse, C_alenable
M_ass positions : I_nclination : O_ffset null ADXL : e_X_it :- KEY ?
The possible inputs are shown in the table below:
Input | Function |
Initiate centring of All components. | |
Initiate centring of the Vertical component only. | |
Initiate centring of the North/South component only. | |
Initiate centring of the East/West component only. | |
Place the instrument into one-second (Short-period) mode. | |
Place the instrument into Broadband (long-period) mode, as configured by the control lines (see section 3.3.4 on page 10). The actual period selected will be reported to the operator after this command has taken effect. | |
Allows the operator to select the default frequency Response of the sensor: i.e. the response that will be selected on power-up and after each centre is completed (but see section 4.3.5). Note that if the default is changed to MSP (medium-short period), Pin T will be low so pulling Pin S low will therefore result in a short period response and vice versa. DO NOT attempt to drive these lines high. | |
Toggle between enabling and disabling Calibration. | |
Print the current Mass position values. | |
Print the current Inclinometer outputs (in three axes). | |
Reset the inclinometer outputs to zero. This command is primarily for factory use and should only be issued when it is known that the instrument is accurately vertical. | |
Exit the command menu. The processor will check the mass positions, perform centring if required and then enter the low-power “sleep” mode. |