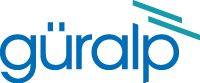
Chapter 8. Appendices
8.1 Connector pin-out
This is a standard 22-pin military-specification “tri-start” bayonet connector, conforming to MIL‑DTL‑38999 series Ⅲ (formerly MIL‑C‑38999), with Amphenol part number TVS07RF-13-35PN-W63. Suitable mating connectors have part-numbers like ***‑13‑35S and are available from Amphenol, ITT Cannon and other manufacturers. |
|
Pin | Function | Pin | Function |
1 | RS232 data input (Rx) | 12 | Busy |
2 | RS232 data output (Tx) | 13 | Serial console RS232 data input |
3 | +12 V DC power input | 14 | Serial console RS232 data output |
4 | Power Ground | 15 | Calibration signal |
5 | E/W Velocity inverting (-) | 16 | Calibration signal return |
6 | E/W Velocity non-inverting (+) | 17 | E/W signal ground |
7 | N/S Velocity non-inverting (+) | 18 | N/S signal ground |
8 | N/S Velocity inverting (-) | 19 | Z signal ground |
9 | Z Velocity inverting (-) | 20 | Short Period mode |
10 | Z Velocity non-inverting (+) | 21 | Initiate Centring |
11 | Calibration enable | 22 | Logic / RS232 ground |
| Wiring details for the compatible socket, ***‑13‑35S, as seen from the cable end (i.e. when assembling). |
8.2 Channel names
When connected to a Minimus, the names of the various output channels of the Certis change according to context, as shown in the tables below.
8.2.1 Analogue channels
Source | Data Stream | Data Record | GCF * | GDI † |
Z velocity, higher rate | 0VELZ0 | S0SeisZA | VELZ0 | 0VELZ0 |
N velocity, higher rate | 0VELN0 | S0SeisNA | VELN0 | 0VELN0 |
E velocity, higher rate | 0VELE0 | S0SeisEA | VELE0 | 0VELE0 |
Z velocity, lower rate | 0VELZ2 | S0SeisZB | VELZ2 | 0VELZ2 |
N velocity, lower rate | 0VELN2 | S0SeisNB | VELN2 | 0VELN2 |
E velocity, lower rate | 0VELE2 | S0SeisEB | VELE2 | 0VELE2 |
Z mass position | 0VELM8 | S0IntZ | VELM8 | 0VELM8 |
N mass position | 0VELM9 | S0IntN | VELM9 | 0VELM9 |
E mass position | 0VELMA | S0IntE | VELMA | 0VELMA |
Calibration return | 0AUXX0 | S0SeisXA | AUXX0 | 0AUXX0 |
Note: * Analogue GCF stream IDs appear in Scream’s source tree under the heading Ainstrument. † GDI stream IDs are prefixed with the serial number of the digitiser.
8.2.2 Digital channels
Source | Data Stream | Data Record | GCF * | GDI † |
Z velocity | CertisZ0_ | CertisZ0_sd | CERSZ0 | CertisZ0_ |
N velocity | CertisN0_ | CertisN0_sd | CERSN0 | CertisN0_ |
E velocity | CertisE0_ | CertisE0_sd | CERSS0 | CertisE0_ |
Z mass position | CertisMassZ_ | CertisMassZ_sd | CERSSZ | CertisMassZ_ |
N mass position | CertisMassN_ | CertisMassN_sd | CERSSN | CertisMassN_ |
E mass position | CertisMassE_ | CertisMassE_sd | CERSSE | CertisMassE_ |
Calibration return | Calibrate_ | Calibrate_sd | CALATE | Calibrate_ |
Z MEMS | AccelerometerZ_ | AccelerometerZ_sd | ACCERZ | AccelerometerZ_ |
N MEMS | AccelerometerN_ | AccelerometerN_sd | ACCERN | AccelerometerN_ |
E MEMS | AccelerometerE_ | AccelerometerE_sd | ACCERE | AccelerometerE_ |
Heading | Heading_ | Heading_sd | HEAING | Heading_ |
PLL phase | PLLPhase_ | PLLPhase_sd | PLLASE | PLLPhase_ |
PLL quality | PLLQuality_ | PLLQuality_sd | PLLITY | PLLQuality_ |
PLL control | PLLControl_ | PLLControl_sd | PLLROL | PLLControl_ |
Pressure | Pressure_ | Pressure_sd | PREURE | Pressure_ |
Relative humidity | RelHumidity_ | RelHumidity_sd | RELITY | RelHumidity_ |
Temperature | Temperature_ | Temperature_sd | TEMURE | Temperature_ |
Note: * Digital GCF stream IDs appear in Scream’s source tree under the heading Dinstrument. † GDI stream IDs are prefixed with the serial number of the Certis.
8.3 Calibration
Güralp force-feedback instruments, like the Certis, do not generally display any significant drift of calibration values. There may be times, however, when you might need to verify the calibration of the instrument for regulatory reasons. A calibration procedure can also be useful if damage to the instrument is suspected.
Calibration of Güralp force-feedback instruments involves injecting a known signal into the circuitry at the point where the feedback system drives the feedback coil. Because the inertial mass and coil geometry are constant, the known signal is equivalent to a known acceleration, to which the response of the instrument can be evaluated.
The Certis can be calibrated using an external signal sources or by using its own, internal signal generator.
8.3.1 Initiating calibration
A calibration can be initiated in three ways. If used with a Minimus, the entire calibration can be performed using the Minimus and Discovery. If a Minimus is not being used, a calibration can be initiated using the serial console or by using the hardware control line.
8.3.1.1 Using a Minimus
To initiate a calibration using a Minimus, open the Discovery software, right-click on the Minimus in the main device list and choose View Web Page (in system browser) from the context menu.
Note: If you are on the same LAN as the Minimus, right-click in the LAN Address column of Discovery’s main window to connect using the LAN address. If you can only connect via a WAN. right-click in the WAN Address column to connect using the WAN address.
When the web interface opens, log in as normal and navigate to the Setup tab. The calibration controls are at the bottom of the Serial Sensor section:
Select the desired calibration type from the Cal Source drop-down menu and the desired amplitude from the Cal Level drop-down menu. Leave the Analogue Out drop-down menu set to Off. For general calibration, we recommend setting the Cal Source to Random and the Cal Level to 100%.
To terminate the calibration, set the Cal Source to Off.
8.3.1.2 Using serial console commands
Open a serial console as described in section 4.3. The following serial console commands are available for controlling calibration:
Command | Action |
cal extern nnn | Initiate a calibration using an external signal. Parameter nnn controls an attenuator that can be used to reduce the amplitude of the signal in units of percent. Specifying 100 for nnn passes the signal through unattenuated while specifying 50 will attenuate the external signal by 3 dB. |
cal reset | Cancels a calibration using an external signal. |
cal sin nnn mmm | Initiate a calibration using an internally-generated sine-wave signal. Parameter nnn controls the amplitude in units of percent. Parameter mmm controls the frequency in units of micro-Hertz (µHz). 1×10⁶ µHz = 1 Hz. For example, the command |
cal tri nnn mmm | Initiate a calibration using an internally-generated triangle-wave signal. Parameter nnn controls the amplitude in units of percent. Parameter mmm controls the frequency in units of micro-Hertz (µHz). |
cal step nnn mmm | Initiate a calibration using an internally-generated square-wave signal. Parameter nnn controls the amplitude in units of percent. Parameter mmm controls the frequency in units of micro-Hertz (µHz). |
8.3.1.3 Using hardware control lines
Calibration can also be initiated using that hardware control lines exposed on its connector. See section 8.1.1 for the relevant pin numbers. Calibrations initiated in this way must use an external signal source.
Before initiating a calibration, connect the external signal source to the Calibration signal pin, relative to the Calibration signal return pin. To initiate the calibration, connect the Calibration enable pin to the Logic / RS232 ground pin and leave the connection in place during the calibration.
To terminate the calibration, break the connection between the Calibration enable pin and the Logic / RS232 ground pin. The external signal source can then be disconnected.
8.3.2 Analysing results
Once a calibration is initiated, open the Discovery software, locate the Minimus in the main device list, right-click on it and select Live View → GDI from the context menu. The Live View window opens.
Note: For clarity, you may wish to turn off the display of any unnecessary streams. This can most easily be done by clicking the top-most check-box (labelled with the serial number of the Minimus) twice. This turns off display of all streams. You can then re-enable the desired streams as described below.
Ensure that the calibration signal and the desired return signals are displayed by expanding the DInstrument section of the stream selection tree and ticking the check-boxes to display the stream ending Calibrate_ as well as one or more of the streams ending CertisZ0_, CertisN0_ and CertisE0_, as desired.
Zoom in or out as necessary in order to display a reasonable period of the calibration data. The longer the period of data captured, the better the results, especially at longer periods.
Hold the left mouse button down while dragging horizontally across the Calibrate_ stream: the area over which you have dragged will be highlighted. Right-click on one or more of the streams ending CertisZ0_, CertisN0_ and CertisE0_, as desired: the highlighted section will be extended.
Right-click in the highlighted section and select Transfer Function from the context menu.
Click OK on the Choose Mode dialogue:
Click Yes or No on the Plot Phase Wrapped dialogue as desired:
until a window is displayed containing two graphs: one of amplitude against frequency and one of phase against frequency. If you are calibrating more than one component, the above sequence of dialogues will be repeated for each component that you selected.
On each graph, the theoretical response is shown in blue and the measured response is shown in red. A set of poles and zeros is computed which matches the measured amplitude and phase response and the average sensor gain over the pass-band is computed and displayed.
In the example graph below, taken part-way through the production process, it can be seen that the phase response is more flat than the theoretical response and the bandwidth is wider than the theoretical response. This instrument will need further attention.